true
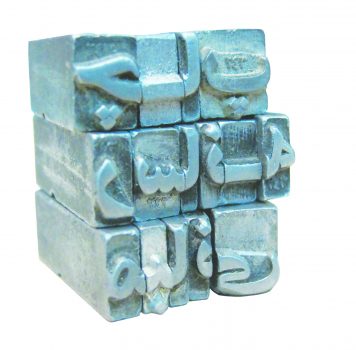
این مقاله به معرفی مرکب های یووی اختصاص پیدا کرده است.
مزیتهای اصلی این نوع مرکبها عبارتند از:
– خشک شدن یا آماده شدن سریع ( ms 100-1 ) به گونهای که امکان انجام مرحلهی پایانی و تکمیلی بلافاصله پس از آن، میسر است،
– عاری از حلال،
– عدم نیاز به هیچگونه عمل خشک کردن در واحد مرکبدهی یا روی نوردها (بدینترتیب نیاز کمتری برای تمیز کردن واحدهای مرکبدهی وجود دارد)،
– گرمایش صفر درجهای یا حداقلی سطح چاپی،
– ثبات مکانیکی و مقاومت شیمیایی بالا.
اما ایرادات وارد به مرکبهای یووی را میتوان اینطور بیان کرد:
– هزینهی این نوع مرکبها بیشتر از مرکبهای چاپی معمولی است،
– طراحی خشککن آن در سطح بالای فنی قرار دارد،
– نیاز به کنترل همه جانبهی مرکب به دلایل کیفی.
مرکبهای یووی ساختار کاملا متفاوتی نسبت به مرکبهای چاپی معمولی دارند. به طور کلی از این نوع مرکبها در چاپ مواد غیرقابل جذب مانند پلاستیکها، ورقههای فلزی و همچنین لیبلها و تولیدات مقوایی پیشرفته استفاده میشود.
مرکبهای یووی در همهی فناوریهای چاپی متداول از جمله فناوری جوهرافشان حضور دارند. مواد تشکیلدهندهی این نوع مرکبها عبارتند از:
– مونومرها
– پری پلیمرها/ اولیگومرها
– رنگدانهها
– افزودنیها
– سینرجیستها (Synergists)
در نتیجه، مرکبهای یووی، هیچ مادهی فراری در خود جای نمیدهند. مونومرها مایع هستند و برای تنظیم ویسکوزیتهی عمل فرآوری از آنها استفاده میشود. مونومرها همراه با پریپلیمرها سیستم رنگ پایه را تشکیل میدهند (شکل ۱۱-۵-۱ را ببینید).
در جریان عمل پرتودهی یووی، پریپلیمرها یا اولیگومرها با مونومرها وارد واکنش میشوند و به پلیمرهای سه بعدی تبدیل میشوند. فتو اینیسیاتورها (Photo – initiators) یا سینرجیستها در جریان عمل پرتودهی یووی به رادیکالها تجزیه میشوند و عمل پلیمریزاسیون آغاز میگردد. این رادیکالها در یک سری واکنشهای شیمیایی، رادیکالهای دیگر را به وجود میآورند و با مونومرها و پری پلیمرها واکنش میدهند.
رنگینهها و افزودنیهای مورد استفاده در مرکبهای چاپی یووی تقریبا با انواع دیگر مرکبهای چاپی هماهنگی دارد. به طور کلی، هنگام عمل فرآوری مرکبهای یووی و جلادهندهها، باید احتیاط نمود تا هنگام تقسیمبندی مرکبها یا جلادهندهها، هیچ قطرهی مرکبی بیهوده بر روی سطح جاری نشود.
این قطرهها ممکن است دستگاه را آلوده و به فضای اطراف تراوش نمایند. تیرگی و به هم ریختگی مرکب به سرعت چاپی، نوع چسب مورد استفاده، طراحی واحدهای مرکبدهی، پوششدهی و دما بستگی دارد. مرکب یووی به دلیل وجود فتو اینسیاتورها (Photo – initiators) بوی خاصی دارد که این بو پس از خشک شدن مرکب تا حد زیادی از بین میرود.
مرکبهایای بی(EB فرآوری شده توسط پرتو الکترون)
با استفاده از مرکبهای ایبی، میتوان فتو اینیسیاتورها را حذف کرد. چون پرتوهای الکترون مستقیما بر چسب واکنشپذیر، اثر میگذارند. لایهی مرکب با ضخامت بالا را میتوان به روش اتصال عرضی درآورد. چون پرتوهای الکترون عمیقا به سطح نفوذ پیدا میکنند و اثرات رنگدانههای مورد استفاده به حداقل میرسد.
مرکبهای خاص: متالیک و پِرلِسنت
آن دسته از مرکبهای چاپی که از رنگدانههای فلزی (متالیک)، رنگدانههای با افکت مروارید رنگین کمانی یا رنگدانههای تداخلی استفاده میکنند، توانستهاند در میان سایر مرکبهای چاپی طلایی یا نقرهای جایی برای خود باز کنند؛ مرکبهایی که به نوعی یک ویژگی فلزگونه دارند. رنگدانههای طلایی – برنزی از آلیاژهای برنجی با نسبتهای مختلف روی و مس به دست میآیند.
آلیاژهای برنج با نسبتهای مختلف روی و مس به دست میآیند. هر چقدر محتویات مس در آلیاژ بیشتر باشد، رنگدانهها قرمزتر به نظر میرسند.
فناوری مورد استفاده در ساخت برنزها، عناصر رنگدانههای فلزی با اندازههای مختلف را قادر میسازد تا با فناوری چاپی مربوطه سازگار شوند. این اندازه در چاپ افست ۵/۳ میکرومتر و در چاپ گراوور و فلکسوگرافی بین ۸ تا ۹ میکرومتر است (در نتیجه، ضخامت لایهی مرکب به طور قابل ملاحظه بیشتر از رنگدانهها یا مرکبهای معمولی است ( Mm 3-1/0)).
در ساخت رنگدانههای نقرهای یا سیلور، فرض میشود که درجه خلوص آلومینیوم ۵/۹۹درصد است. پس از ذوب آلومینیوم در کورههای القایی، مایع مذاب تحت تاثیر یک جریان هوای فشرده قرار میگیرد. محصول نهایی تودهای از ذرات فلزی است که سطح صیقلی دارند.
این مرکبها مانند مرکبهای معمولی چاپ افست با استفاده از روش اکسیداسیون و تبخیر خشک میشوند.
جدیدترین پیشرفتهای به دست آمده مربوط است به مرکبهای چاپی طلایی و نقرهای که روی ورنیهای پخشی قابل رقیق شدن در آب ساخته و از طریق واحدهای روکشدهی ارسال میشوند. این مرکبها با جذب در سطح چاپی و تبخیر بخار آب موجود در مرکب خشک میگردند. مرکبهای جدید، درخشانی فوقالعادهای نسبت به مرکبهای چاپی طلایی و نقرهای معمولی دارند.
از مرکبهای چاپی با رنگدانههای فلزی در چاپ گراوور و فلکسوگرافی نیز استفاده میشود. ساختار این مرکبها همانند رنگدانههای آلی و غیرآلی است.
۲-۲-۵-۱ مرکبهای چاپی افست
وجود مرکبهای چسبناک با ویسکوزیتهی بالا، برای چاپ افست ضروری است (ویسکوزیتهی دینامیک۱۰۰Pa.s-40 :η) مرکب باید به گونهای ساخته شده باشد که اجزای خشککنی موجود در مرکب بلافاصله پس از پخش روی نوردها در واحد مرکبدهی یا ایستگاههای انتقالی بعدی مانند پلیت یا لاستیک چاپی خشک و سفت نشوند. وانگهی، مرکب چاپی مورد استفاده در چاپ افست متداول باید قادر باشد که بخشی از محلول یا آب افست را ذخیرهسازی کند.
این بخش از محلول از طریق تماس با پلیت یا مستقیما توسط واحد آبزنی جذب میشود. (در چاپ افست خشک، میتوان روغن سیلیکونی را به مرکب اضافه نمود تا اطمینان حاصل کرد که فضاهای غیر چاپی تصویر به مرکب آغشته نشدهاند.) در چاپ افست، لایههای فوقالعاده نازک با ضخامت تقریبی ۵/۰ تا ۵/۱ میکرومتر به روی سطح منتقل میشوند. مرکبهای افست از اجزای زیر ساخته میشوند (نسبتهای وزنی):
– وارنیش یا ورنی پایه روغن به طور کلی در برگیرندهی رزینهای سخت (۵۰-۲۰ درصد) همراه با نسبتهایی از کولوفون، رزینهای آلکیدی (۲۰-۰درصد) و مقداری روغن گیاهی مانند روغن سویا، روغن چوب و همچنین روغنهای معدنی (۴۰-۲۰ درصد) و عناصر خشککنی مختلفی است (۲< درصد).
– میزان رنگدانهی مورد استفاده با توجه به رنگ، بین ۱۰ تا ۳۰درصد است.
– افزودنیها، سهمی در حدود ۱۰درصد در ترکیب مرکبهای افست دارند.
مواد افزودنی مورد استفاده در این مرکب ها عبارتند از:
– کاتالیزورهای خشککن (ترکیبی از کبالت، منگنز و دیگر فلزها)،
– موم برای بهبود مقاومت در برابر سایش و جلوگیری از ایجاد لکه،
– موادی برای جلوگیری از خشکشدن زود هنگام و ایجاد رویه بر روی سطح در بطری یا مخزن مرکب،
– روغنهای سیلیکون برای مرکبهای چاپی مورد استفاده در چاپ افست خشک.
به دلیل وجود امکانات و شرایط متنوع در محصولات چاپی نهایی و ماهیت سطوح چاپی، میزان محتویات مواد سازندهی مرکب متغیر است. به علاوه، هنگام ساخت مرکب چاپی باید شرایط و امکانات خاص چاپ افست مورد توجه قرار گیرند. در مرکبهای چاپی افست، موارد زیر از اهمیت خاصی برخوردارند:
– شفافیت بالا (به دلیل ترکیب کاهشی مرکبها در چاپ بیش از حد)؛
– ویژگیهای لازم مربوط به قابلیت چاپ و عملکرد چاپی مانند مشخصههای مربوط به روانی مرکب، خشککردن، درخشانی، امولسیونسازی، عملکرد کاغذ، مقاومت در برابر سایش؛
– پذیرش مرکب سطح و مناسب بودن مرکب با چاپ تر روی تر؛
انواع مختلفی از مرکبهای چاپ افست در جدول ۷-۵-۱ تقسیمبندی و توضیح داده شدهاند.
۳-۲-۵-۱- مرکبهای چاپ گراوور
تفاوت اصلی بین مرکب چاپی گراوور و افست، ویسکوزیته یا درجهی غلظت است. گراوور به مایعی نیاز دارد که بتواند تصویر شکلدهندهی سلولهای سیلندر گراوور را در سرعت بالا پر کند.
واحد مرکبدهی گراوور، «کوتاهترین» واحد مرکبدهی بین تمامی واحدهای مرکبدهی مورد استفاده در فناوریهای چاپی متداول است (کوتاهترین مسیر برای مرکب از مخزن مرکب تا کاغذ). این واحد مرکبدهی تنها شامل یک محفظهی تغذیهی مرکب است که مرکب را مستقیما به پلیت چاپی و تیغهی داکتر را میرساند. واحد مرکب دهی گراوور یک سیستم بسته است که استفاده از مرکب با ویسکوزیتهی فوقالعاده پایین را فراهم میآورد.
ساخت و ترکیب مرکبهای گراوور در مقایسه با مرکبهای افست سادهتر است. دامنهی مرکبهای قابل استفاده در گراوور وسیعتر است و ترکیب شیمیایی آنها به دلیل انتقال مستقیم مرکب امکان دسترسی به گسترهی متنوعتری را میسر میسازد.
«حلالها» در گراوور، اهمیت ویژهای دارند؛ آنها ویسکوزیتهی مرکب را در حد پایین نگه میدارند و در غلظت مرکب یا رنگدانه تغییراتی ایجاد میکنند.
عوامل زیر در انتخاب حلالها مهم شمرده میشوند:
– نقطه جوش
– عدد تبخیر
– نقطهی اشتعال
– حریم احتراق و انفجار
– بو
– کار به روشی ایمن
– سازگاری زیستمحیطی
باید از حلالهای کاملا متفاوت در چاپ و بستهبندی گراوور و چاپ گراوور انتشاراتی استفاده شود. این مسئله اساسا ناشی از شرایط و امکانات متفاوت بستهبندیهای مختلف است.
مهمترین حلالهای مورد استفاده در گراوور انتشاراتی عبارتند از:
– تولوئن (تولوئن خالص حاوی کمتر از درصد۳/۰ بنزن)
– گزیلن (Xylene)
– الکلهای نفتی (در بسیاری از مواد به دلیل قابلیت اشتعالپذیری، استفاده از آن مجاز نیست).
«تولوئن» یک فرآوردهی پتروشیمی و یک مایع بیرنگ و قابل اشتعال است که یک حلال ایدهآل محسوب میشود. این حلال، ذرات موجود در اطراف رنگدانهها را حل میکند. این ذرات را میتوان دوباره در یک سیستم بازیافت به دست آورد. تولوئن با صرف انرژی اندکی خشک میشود و با قیمت نسبتا مناسبی در دسترس قرار دارد. اما چون با سرعت کمتری خشک میشود، امروز به ندرت از آن در چاپ گراوور استفاه میشود.
مهمترین حلالهای چاپ بستهبندی گراوور عبارتند از:
– اتانول (الکل اتیلدار)
– استات اتیل (اتِر استیک)
– آب
استفاده از مرکبهای چاپی که میتوان آنها را به کمک آب رقیق کرد، در گراوور انتشاراتی با فناوریهای امروز، در جایگاه دوم قرار دارد. به دلیل شرایط متفاوت و گستردهی چاپ بستهبندی گراوور (مثلا عدم واکنشپذیری با محتویات یا تغییر در بو)، از متفاوتترین حلالهای آلی برای تولید مرکب چاپی استفاده میشود.
۴-۲-۵-۱٫ مرکبهای چاپی فلکسوگرافی
مرکبهای فلکسوگرافی، از نظر ویسکوزیته شباهت بسیاری به مرکبهای گراوور دارند. دامنهی ویسکوزیتهی آنها بین ۰۵/۰ تا ۵/۰ Pa. s است و قادرند لایه مرکبی به ضخامت ۱ میکرومتر تشکیل دهند. مرکبهای فلکسوگرافی از طریق یک واحد مرکبدهی به روی پلیت چاپی انعطافپذیر منتقل میشود.
این واحد مرکبدهی در بردارندهی یک تیغهی داکتر همراه با نورد آنیلوکس است. ویسکوزیتهی مرکب، نقش مهمی در دستیابی به یک کیفیت خوب چاپی دارد.
شرایط مورد نیاز عبارتند از: عدم فشار مرکب روی لبههای فضاهای تصویری برجسته، ضخامت کافی و مناسب مرکب، تقسیم خوب مرکب و پر کردن سلولهای روی نورد شابلون. تعداد رنگدانههای متفاوت برای مرکبدهی در مرکبهای فلکسوگرافی بسیار بالاست که این مسئله منجر به موارد مصرف و کاربردهای گوناگونی میشود.
همانند چاپ گراوور، نوع حلال نیز نقش مهمی در چاپ فلکسوگرافی ایفا میکند. حلال پس از انتقال به روی سطح با استفاده از گرما تبخیر میشود و لایه مرکب خشک باقی میماند. در چاپ رنگی باید یک مرحله خشک کنی میانی، پس ماندهی مرکب را خشک کند. به طور کلی، حلالهای مورد استفاده در چاپ فلکسوگرافی عبارتند از:
– استات اتیل
– الکل
– آب
اساسا از رنگدانهها به عنوان عوامل رنگی استفاده میشود. در چاپ بستهبندی، مرکبهای حاوی آب مورد استفاده قرار میگیرند. اما در چاپ لیبل، مرکبهای یووی پرمصرفترین مرکبها هستند.
۵-۲-۵-۱- مرکبهای چاپی لترپرس
در چاپ لترپرس (که در بعضی موارد مورد استفاده قرار میگیرد)، از مرکبهای ویسکوز (۱۵۰Pa.s-50 = η)استفاده میشود. مواد تشکیلدهندهی اصلی این مرکبها، رنگدانههای آلی و غیرآلی و مومها هستند. مرکبهای لترپرس، روی کاغذ و مقوا همانند مرکبهای چاپی افست به روش فیزیکی یعنی از طریق جذب و به روش شیمیایی با استفاده ازروش اکسیداسیون خشک میشوند.
هنگام چاپ بر روی مواد غیر جاذب مانند ترانسپارنت یا کاغذ متالیک، خشککردن تنها از طریق اکسیداسیون، هنگام به کارگیری «مرکبهای فویلی» انجام میشود.
در چاپ رولی روزنامهای مبتنی بر فناوری چاپی لترپرس، مرکبهای چاپی با ویسکوزیتهی متوسط کاربرد دارند. عناصر اصلی تشکیلدهندهی این مرکبها، رنگدانههای مشکی کربنی ارزان و روغنهای معدنی هستند. در اینجا، خشک کردن تنها به روش فیزیکی و از طریق جذب مرکبها به کاغذ روزنامهی فوقالعاده جاذب صورت میپذیرد.
۶-۲-۵-۱ مرکبهای چاپی اسکرین
چاپ اسکرین در مقایسه با دیگر فناوریهای چاپی، متنوعترین دامنهی کاربرد را نسبت به سطوح چاپی دارد و میتوان آن را به چهار فضای تولیدی و چاپی تقسیم کرد:
– چاپ اسکرین تجاری برای رسانههای تبلیغاتی گوناگون؛
– چاپ سیلک اسکرین که از آن به عنوان سریگرافی یاد میشود؛
– چاپ اسکرین صنعتی مثلا چاپ بر روی بطری، تیوب و فنجان؛
– فرآیندهای ویژه مثلا چاپ روی پارچه یا تخته مدارهای چاپی برای مدارهای الکترونیکی و غیره.
دیگر سطوح چاپی ممکن علاوه بر مقوا و کاغذ، شامل پلاستیک، شیشه، فلز، پارچه و غیره هستند. ویژگیهای فیزیکی و شیمیایی متنوع این مواد، دلیل وجود انواع مختلف مرکبهای در دسترس در چاپ اسکرین است.
هنگام چاپ روی مواد پلاستیکی، مرکبهای چاپی اسکرین از نظر مواد ترکیبی شبیه به مرکبهای گراوور و فلکسوگرافی هستند. ویسکوزیتهی انتخابی باید با مرکب مورد نظر، ضخامت لایه و ظرافت توری تطابق داده شود.
خشک کردن با تبخیر حلال
خشک کردن با تبخیر حلال فرار صورت میپذیرد و با ورود هوای گرم سرعت آن افزایش مییابد. با این حال، برای کاغذ و مقوا، مرکبهای چاپی مات و براق روغنی یا مومی مورد استفاده قرار میگیرند. این مرکبها، اغلب در یک فرآیند اکسایشی خشک میشوند. گاهی اوقات،مرکبهای یووی در چاپ اسکرین کاربرد دارند.
یکی از ویژگیهای چاپ اسکرین این است که در آن امکان انتقال یک لایه مرکب ضخیم ۱۲ میکرومتری و بیشتر نیز وجود دارد.
۷-۲-۵-۱مرکبهای چاپ بالشتکی
از چاپ بالشتکی به عنون یک فناوری چاپ گراوور غیر مستقیم یاد میشود که کاربرد ویژهای در چاپ سطوح ناهموار و مشکل دارد. در این فناوری چاپی، تصویر چاپی از طریق یک پلیت گراوور به پَد یا تامپون پلاستیکی منتقل میشود.
این پَد یا تامپون پلاستیکی تصویر چاپی را به سطح میرساند. مرکبهای چاپ بالشتکی کاملا شبیه به مرکبهای مورد استفاده در چاپ اسکرین است اما ویسکوزیتهی آن کاهش یافته است. تجمع رنگدانهها در این نوع مرکبها بالاست.
به همین دلیل تنها لایههای نازک مرکب را میتوان منتقل کرد. مرکبهای چاپ بالشتکی معمولا به دلیل وجود حلالهای فرار به سرعت خشک میشوند. اما با این حال، با توجه به نوع سطح چاپی، از خشککنندههای شیمیایی هم استفاده میشود.
برای هر سطح چاپی، به نوع خاصی از مرکب نیاز است. به همین دلیل، مانند چاپ اسکرین، عمل چاپ روی سطوح مختلفی از جمله چوب، لاستیک، پلاستیک، چرم، شیشه، چینی و سطوح روکشدار انجام میشود. معمولا چاپکار باید آزمایشهایی انجام دهد تا چسبندگی مرکبها را کنترل نماید.
۸-۲-۵-۱- مرکبهای مورد استفاده در فناوری چاپی غیرتماسی
الکتروفتوگرافی
در الکتروفتوگرافی (شکل ۱۲-۵-۱ را ببینید)، از «تونر» به عنوان مادهی رنگی یاد میشود. همانطور که در تصویر ۱۳-۵-۱ نشان داده شده، میتوان تونرها را به تونرهای پودری و تونرهای مایع تقسیمبندی کرد.
اجزای تونر به تدریج در واحد به روش الکترواستاتیک شارژ میشوند و به کمک بعضی از قسمتهای تصویریهادی حساس نسبت به نور که با بار مخالف شارژ شدهاند، جذب درام میگردند. انتقال ازهادی حساس نسبت به نور به سطح چاپی توسط نیروهای الکترواستاتیک صورت میپذیرد.
مهمترین کاربرد تونرها در دستگاههای کپی و چاپگرهای الکتروفتوگرافی است. به طور کلی، «تونرهای پودری» به کمک حرارت (نوردهای حرارتی، رادیاتورهای IR) و فشار روی کاغذ تثبیت میشوند.
در سیستمهای دوجزئی امروز، تونر از طریق حاملها (اجزای حامل مغناطیسی) آورده میشود. یک نورد مغناطیسی چرخان، این حاملها را روی نورد ظاهرکننده نگه میدارد. اجزای تونر شارژ میشوند و سپس به حامل میچسبند. به ترکیب تونر و حامل، داروی ظهور میگویند.
تونر
تونر، یک مادهی مصرفی است، این در حالی است که مادهی حامل در سیستم تغذیهی مرکب باقی مانده میماند. تونرها با مشخصات فرآیندهای جداگانهی مدلهای چاپگر و دستگاه کپی تطبیق داده میشوند. نمیتوان تونرهای خشک رنگی (تونر پودری) را با تونر دیگر به منظور دستیابی به یک رنگ جدید ترکیب کرد.
تونرهای خشک معمولا در یک فرآیند گداختی – سایشی تولید میگردند. در این فرآیند، به اجزای تونر یک شکل کم و بیش مشخص، داده میشود (شکل ۱۴-۵-۱). اما روش جدیدتر این کار، ترکیب مستقیم شیمیایی (فرآیند پلیمریزاسیون) است که اجزای کروی با قطرهای یکسان تولید میکند. ضخامت لایهی تونرهای خشک بر روی کاغذ پس از تثبیت بین ۶ تا ۱۵ میکرومتر است. اساسا، تونرهای تک جزئی «مغناطیسی» همانند سیستمهای دو جزئی توضیح داده شده ساخته میشوند اما ذرهی تونر خود شامل یک بخش ظهور مغناطیسی (اکسید آهن) است.
این ذرات تونر بزرگتر و در حدود ۱۲ تا ۲۰ میکرومتر هستند.
تونرهای رنگی مناسب را تنها میتوان به میزان محدود برای چاپ رنگی تولید کرد. اگر اکسید آهن درصد بالایی از حجم تونر را به خود اختصاص دهد، دستیابی به رنگهای روشن و نیمه شفاف مشکل میشود. تونرهای تک جزئی «الکترواستاتیکی» به ذرات حامل نیاز ندارند. ذرات تونر به کمک میدانهای الکترواستاتیک کنترل شده منتقل میگردند. تنها در سرعتهای نسبتا پایین، میتوان از این تونرها استفاده کرد.
در رابطه با «تونر مایع»، عناصر رنگی (معمولا رنگدانهها) در یک مایع پایه و اصلی ترکیب میشوند. انتقال ذرات بارگذاری شده به روی سیلندر تصویرسازی از طریق نیروهای الکتریکی فعال در میدان به وقوع میپیوندد. در تونرمایع، تراکم ذرات تنها در حدود ۵درصد است و برای چاپ باید آن را افزایش داد.
اگر بخواهیم به طور ایدهآل فکر کنیم، تنها ذرات تونر باید به کاغذ برسند؛ در نتیجه مایع پایه و اصلی را باید از ترکیب جدا کرد. ذرات تونر مایع کوچکتر (در حدود ۱ تا ۲ میکرومتر) از ذرات تونر پودری خشک هستند. ذرات کوچک امکان دستیابی به لایهی نازکتر مرکب را فراهم میآورند و وضوح بالاتر باعث میشود که تصویر کیفیتی شبیه به کیفیت افست داشته باشد.
با ترکیب میتوان رنگهای خاص تولید کرد. تونرهای مایع در مقایسه با تونرهای خشک، کاربرد کمتری دارند. در مقایسه با تونرهای خشک، تولید و تهیهی تونرهای مایع مشکلتر است. در اینجا ویسکوزیته، تقریبا در حدود ۱۵mPa. s است.
جوهرافشان
مرکبهای جوهرافشان، ویسکوزیتهی پایینی دارند(۳۰ mPa. s تا۱ = η). در جوهرافشان، جوهرها و بیشتر رنگدانهها کاربرد دارند. مرکبها باید به خوبی فیلتر شده باشند تا ناخالصیها، کانالهای کوچک و نازلهای پرینت هد را مسدود نکنند.
با توجه به فناوری مورد نظر و سطح چاپی، مایعات مختلف حامل مورد استفاده قرار میگیرند:
* جوهرافشان قطرهای:
– جوهرافشان حرارتی: آبی،
– جوهرافشان پیزو: آبی، روغنی، مومهای مذاب برای چسب داغ، پلاستیکهای مایع مرکبها برای مرکبهای یووی
* جوهرافشان پیوسته: آب، MEKs (متیل اتیل کتون)
به دلیل ویسکوزیتهی پایین مرکبها، نتیجهی چاپی تا حدود زیادی به سطح چاپی بستگی دارد. این مرکبها تمایل دارند تا رنگ پس دهند و به داخل سطح نفوذ پیدا کنند و یا در رابطه با سطوح غیر جاذب، به شکل مرمری درآیند.
علاوه بر این، سطح حالت هندسی خود را (تشکیل موجها)، به دلیل نسبت بالای مایع (۹۰ تا ۹۵درصد)، تغییر میدهد. با استفاده از بعضی روکشهای خاص، میتوان تا حدودی زیادی از میزان مشکلات گفته شده کاست. این روکشها مایع را ذخیره میکنند و از پخش آن جلوگیری به عمل میآورند.
لایههای مرکبهای آبی، روغنی یا MEK بسیار نازکند (میکرومتر ۵/۰> )، اما از طرف دیگر مرکبهای چسب داغ و یووی، به دلیل میزان کم مایع، لایههای نسبتا ضخیم تشکیل میدهند (میکرومتر۱۰> ).
true
true
https://sanatpanjom.ir/?p=2644
true
true